As the world accelerates towards electrification and rapidly deploys clean energy technologies, the demand for efficient and sustainable energy storage solutions has become increasingly critical. Lithium-ion batteries are at the forefront of this revolution, and there are two essential components that define a battery’s specifications and performance – the anode and the cathode.
This installment of the Battery Recyclopedia will briefly describe battery cathodes and anodes, the materials they are made from, how they are manufactured, the importance of incorporating recycled content, and their significance in promoting electrification and clean energy.
What are battery anodes and cathodes?
A cathode and an anode are the two electrodes found in a battery or an electrochemical cell, which facilitate the flow of electric charge. The cathode is the positive electrode, where reduction (gain of electrons) occurs, while the anode is the negative electrode, where oxidation (loss of electrons) takes place.
During the charging process in a battery, electrons flow from the cathode to the anode, storing energy that can later be used to power devices
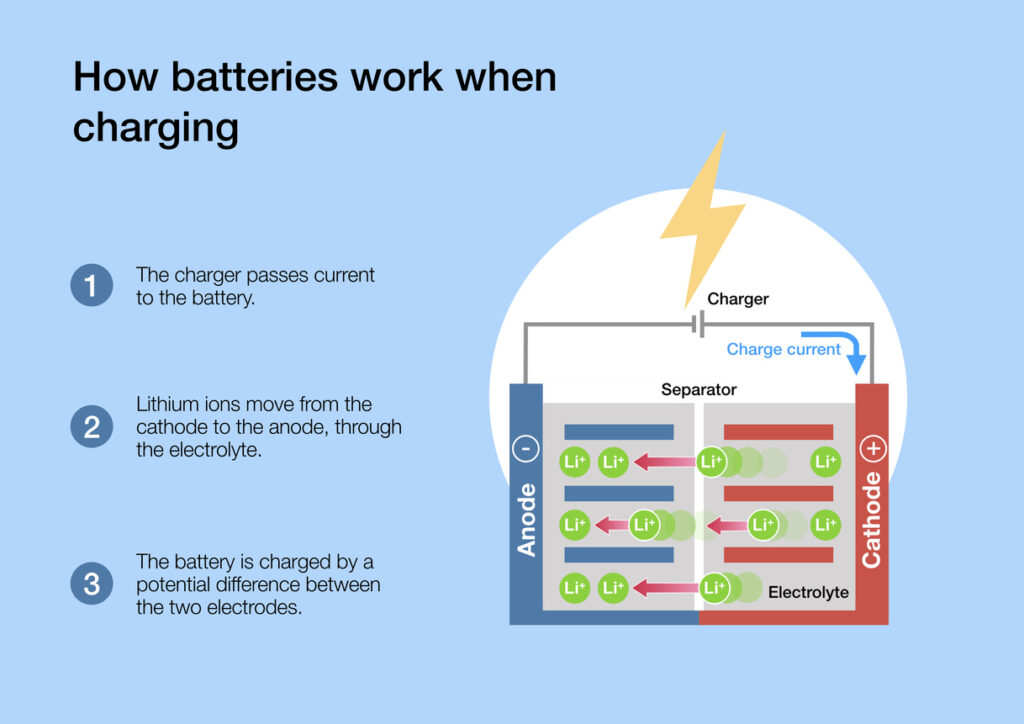
What materials are used in anodes and cathodes?
Cathode active materials (CAM) are typically composed of metal oxides. The most common cathode materials used in lithium-ion batteries include lithium cobalt oxide (LiCoO2), lithium manganese oxide (LiMn2O4), lithium iron phosphate (LiFePO4 or LFP), and lithium nickel manganese cobalt oxide (LiNiMnCoO2 or NMC). Each of these materials offers varying levels of energy density, thermal stability, and cost-effectiveness.
Anode active materials (AAM), on the other hand, are generally made from carbon-based materials like graphite, silicon, or a combination of both. Graphite is the most commonly used anode material due to its high electrical conductivity, low cost, and stable structure. Silicon anodes offer higher energy density but face challenges in terms of volume expansion and shorter cycle life. Some anode iterations will also ‘dope’ graphite anodes with a small amount of silicon to improve performance characteristics and energy density.
The materials and metals used in cathode manufacturing can account for 30-40% of the cost of a lithium battery cell, whereas the anode materials will typically represent about 10-15% of the total cost

Manufacturing anodes and cathodes
While each manufacturer will have its own process and often its own recipe, there are typically several steps involved in the manufacture of anodes and cathodes.
First, the necessary cathode and anode materials will be synthesized into the desired compounds to create the electrode. This mixture of compounds is referred to as cathode active materials (CAM) and anode active materials (AAM), respectively.
These synthesized materials are then ground into a fine powder and mixed with binders and solvents to create a ‘slurry’ ready for further processing.
Next the slurry mixtures will be coated onto a metal foil – usually aluminum foil for the anode and copper foil for the cathode – and dried in an oven to secure the material to the foil and remove remaining solvents.
After drying, the foils undergo a ‘calendering’ process, where they are passed through a series of rollers to compress and smooth the coating, ensuring uniform thickness and proper adhesion.
The resulting coated anode and cathode foils are then ready to be cut to size and combined with other components to build a lithium-ion battery cell.
Recycled content in cathode and anode materials
While a battery’s performance will slowly degrade over time, the metals and valuable materials that go into the battery are not actually being depleted.
As the demand for lithium-ion batteries grows, so does the need for sustainable and cost-effective materials, and one of the ways to achieve this is by increasing the use of recycled content in the manufacturing process of cathode and anode materials. The content for recycling can come from end-of-life batteries or from manufacturing scraps.
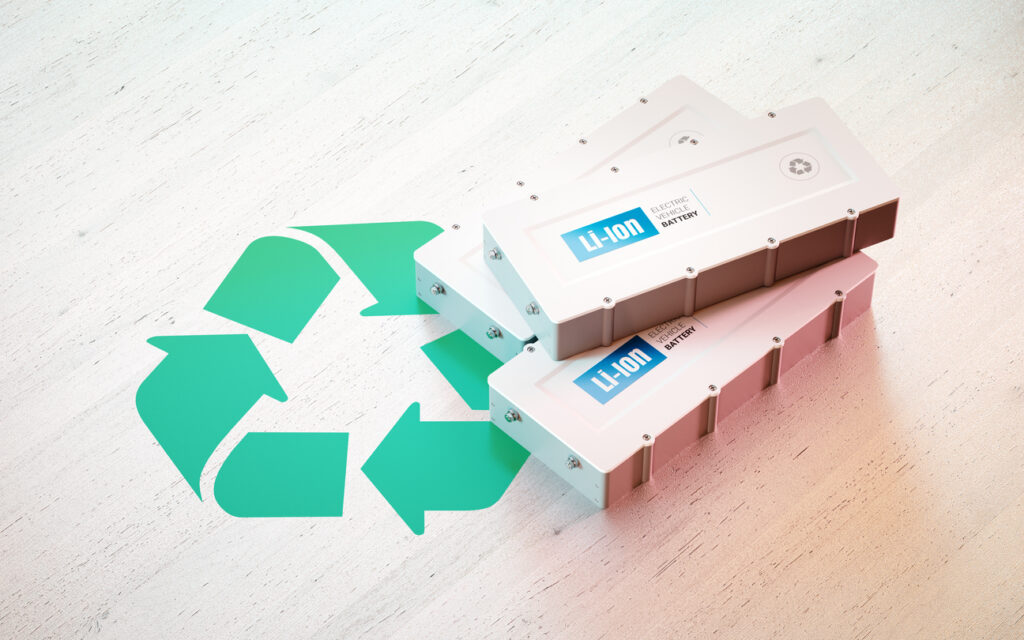
Using recycled materials in battery manufacturing offers several benefits:
Resource conservation: Recycling reduces the need for mining and extraction of raw materials, preserving natural resources and minimizing environmental impacts.
Reduced carbon footprint: The recycling process can require less energy than extracting and processing raw materials, leading to lower greenhouse gas emissions.
Waste minimization: As the number of end-of-life batteries increases, recycling can help minimize the accumulation of hazardous waste in landfills.
Cost-effectiveness: Using recycled materials may be more cost-effective than sourcing raw materials, providing an economic incentive for battery manufacturers to adopt sustainable practices.
Supply Chain Integrity: Working with recycled materials enables a secure domestic supply of the minerals and metals used to make cathodes and anodes. Companies can also ensure that raw materials were ethically sourced.
Recycled Battery Materials: Paving the way for electrification and clean energy
Incorporating recycled content in the production of cathode and anode materials is a vital step towards achieving electrification and clean energy goals on a global scale. By reusing valuable materials from end-of-life batteries and manufacturing scraps, we can conserve natural resources, reduce waste, and minimize the environmental impact of mining and processing raw materials.
Embracing such sustainable and responsible practices in battery manufacturing can lead to a greener, more efficient energy storage industry, ultimately supporting the transition to renewable energy sources and electric transportation.