If you have read an article about lithium-ion battery recycling or mining for critical metals, you have probably come across the term ‘black mass.’
In this entry to the Battery Recyclopedia, we’ll define black mass, what it is made of, and why it is so important to the circular battery economy.
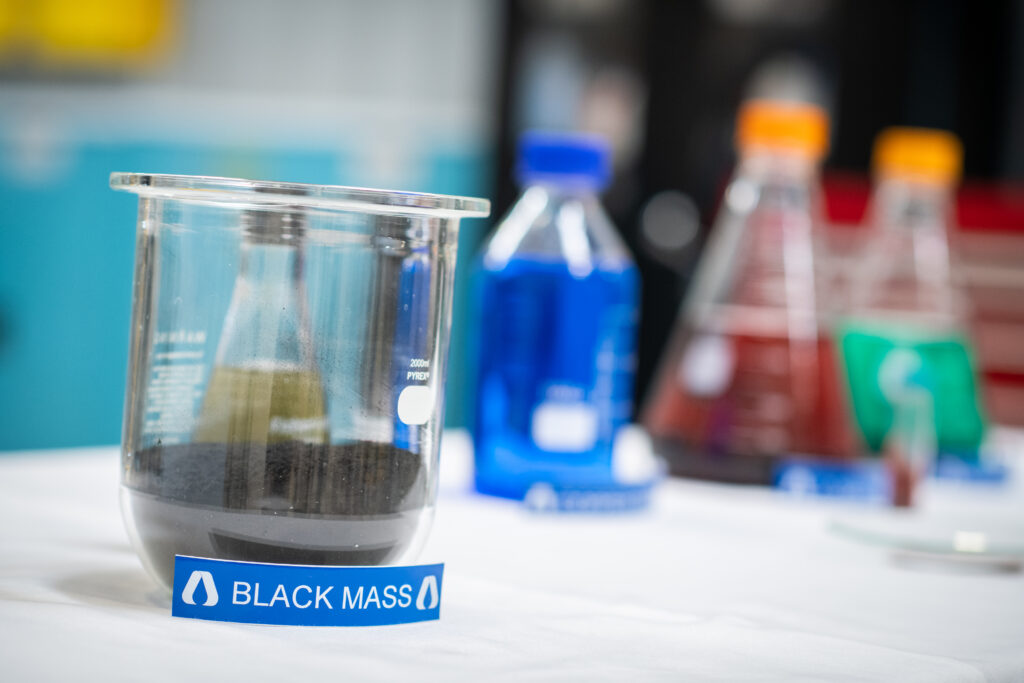
What is black mass?
Lithium-ion batteries are comprised of valuable metals such as lithium, copper, manganese, cobalt, and nickel. Once a battery is retired, the batteries can be collected, fully discharged, then shredded and base metals are separated to prepare them for recycling. (The companies that collect and process batteries into black mass are sometimes referred to as ‘shredders’).
This shiny, metallic mixture is what is called ‘black mass’—and it contains all the valuable metals that make up battery anodes and cathodes (the most expensive parts of a battery). The typical black color is due to the high concentrations of graphite contained in the anodes of batteries, which has a very dark black color.
Black mass makes up about 40-50% of the total weight of an EV battery. Materials like the binder, copper, electrolytes, plastics, aluminum, and steel have been physically separated out by shredders before being recycled. The remainder is a mixture of material that appears black in color with silvery metallic flecks sprinkled throughout.
Recyclers (like Aqua Metals) will accept the black mass from pre-processors and convert it back into saleable commodity metals—thereby circularizing the battery metal supply chain.
How is black mass made?
There are two main processes to producing black mass:
- Pyrometallurgy: some black mass producers will use high-temperatures to burn off unwanted materials like plastics and remaining electrolyte. This can create hazardous emissions and waste that must be captured or mitigated, and result in less recovered material.
- Hydrometallurgy: many producers use solution-based techniques—using water, chemicals and electricity to crush and separate the materials from a battery. This eliminates the need for polluting furnaces and energy intensive processing, creating a lower-carbon black mass.
[Aqua Metals specifically partners with producers that use non-pyro processes in order to create black mass to meet our own objectives for creating low-carbon recycled materials.]
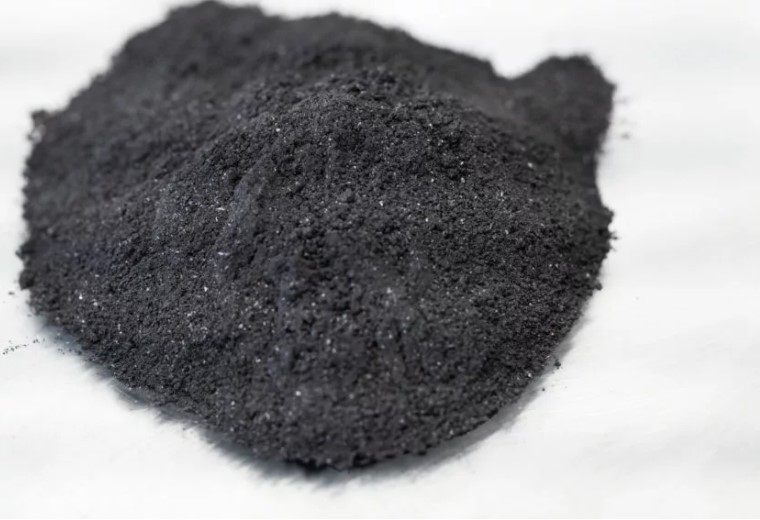
What metals are in a ton of black mass?
The exact composition of black mass can vary considerably based on a number of factors.
To start, there are many different types of lithium-ion batteries and manufacturing scrap forms, which will revert back to a mix of different elements and different ratios, including lithium, nickel, iron, titanium, copper, cobalt, manganese, and others (their use of lithium metal is the commonality).
Each manufacturer also has their own specific ‘recipe’ for their cathodes, cell type/form factors, as well as module type and pack assembly for different applications (cell phones, laptops, electric vehicles, etc.).
Currently, the most popular types of lithium-ion batteries in the world incorporate significant amounts of nickel, cobalt, lithium, and manganese—so black mass produced today will typically have varying concentrations of each.
A sample black mass composition could include (% by weight):
- Lithium compounds: 2-6%
- Cobalt: 5-20%
- Nickel: 5-15%
- Copper: 3-10%
- Aluminum: 1-5%
- Iron: 1-5%
- Manganese: 2-10%
- Remainder: Graphite, with iron, aluminum and copper flakes
Again, it’s worth noting that these percentages can vary depending on the specific source and recycling method used. In addition, the exact composition of lithium black mass from recycled batteries may depend on factors such as the age and condition of the batteries being recycled, as well as the efficiency of the production process.
Recycling companies like Aqua Metals purchase black mass on the open market based on the assessed metals content, and the composition of other materials like aluminum and copper (discounted from their market value in pure form).
Overall, black mass is an essential step in the recycling of lithium-ion batteries, and ensuring that it is produced responsibly with limited emissions and hazardous waste is critical to building a sustainable circular supply chain for battery metals.