As lithium-ion batteries become increasingly prevalent in our daily lives, powering electric vehicles and portable electronics, the need for cost-effective and sustainable recycling methods has never been more important.
This entry in the Battery Recyclopedia serves as a primer to the many types of lithium-ion battery recycling, the basic methodology, benefits, and challenges.
Pyrometallurgy describes a suite of high-temperature processing technologies (typically up to 1400°C) that entail roasting lithium-ion batteries in a furnace to extract valuable metals such as cobalt, nickel, and copper. This technology was repurposed from the mining industry as a way to collect metals from raw ore and rocks. The high temperatures used break down the battery components allowing for the separation and collection of the desired metals based on thermodynamic reactions.
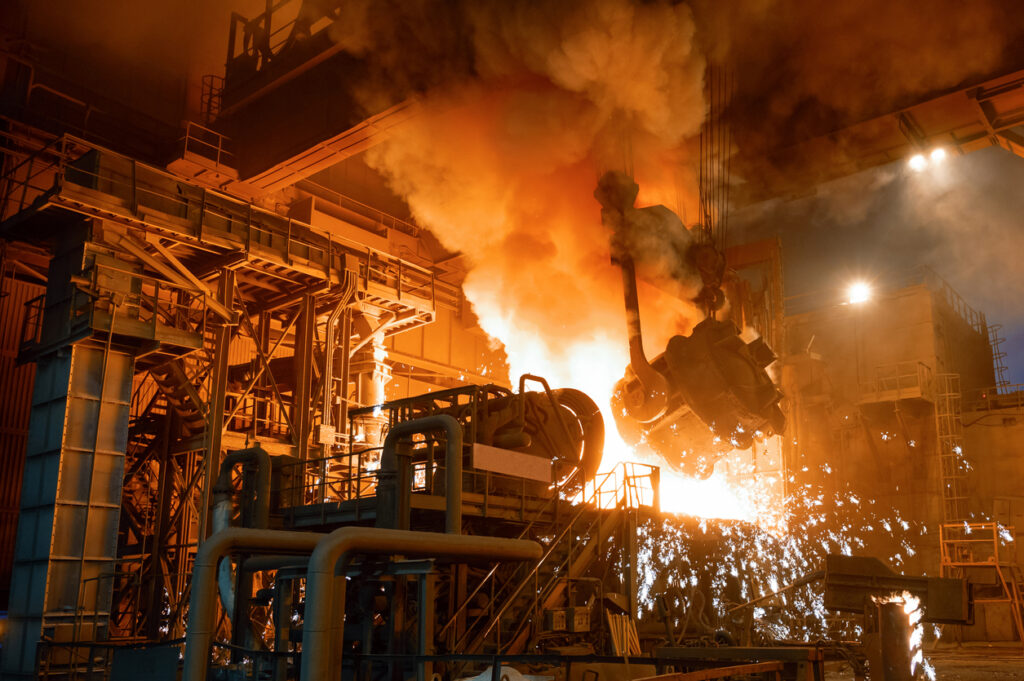
However, pyrometallurgy recycling has significant drawbacks, as it is energy-intensive, consuming large amounts of fossil fuels, and generates considerable amounts of hazardous fluoride and carbon dioxide emissions, which can diminish human health and contribute to global warming.
The graphite and binders in batteries are destroyed instead of recycled, and battery metals are sorted into either the matte (Ni/Co/Cu/Fe) or the slag (Li/Mn/Ca/O). There are unproven technologies that could recover lithium and manganese from the slag, but they are expensive and require even more energy to implement.
Consequently, despite being a mostly straightforward method for metal recovery, pyrometallurgy’s negative environmental impacts, low recovery rates, and significant waste prevent it from being a long-term viable and sustainable option for lithium-ion battery recycling.
Hydrometallurgy is a chemical recycling process that involves the use of acids or other solvents to leach metals from spent lithium-ion batteries. By dissolving the metals in a liquid solution, they can be subsequently precipitated out of solution individually and recovered for reuse. These chemical reactions do not produce pure metals, but instead typically produce various metal salts (like nickel sulfate) which may require additional processing to be used in battery manufacturing.
While hydrometallurgy boasts a lower energy consumption compared to pyrometallurgy, it unfortunately generates significant amounts of sulfate waste as a byproduct of chemical reactions that must be landfilled and pose environmental and public health risks. Additionally, this method is less efficient at recovering certain metals, such as lithium, which is an essential component in the production of new lithium-ion batteries, making it a less optimal choice for comprehensive battery recycling.
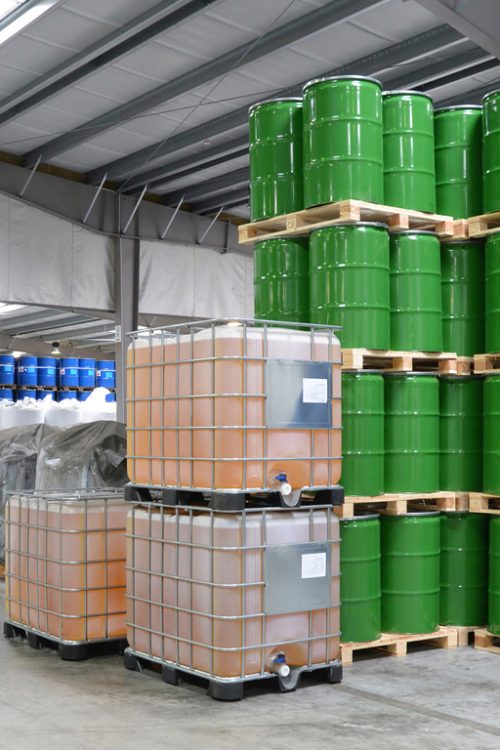
Electro-hydrometallurgy is an innovative recycling method that merges the principles of hydrometallurgy and electrochemistry to recover valuable metals from lithium-ion batteries.
In this process, an electric current is applied to a leaching solution containing dissolved metals, enabling the selective extraction and recovery of valuable metals such as cobalt, nickel, and lithium. These materials are recovered as pure metals—instead of alloys or salts—so they can go right back into the supply chain for battery manufacturing or other advanced industrial applications.
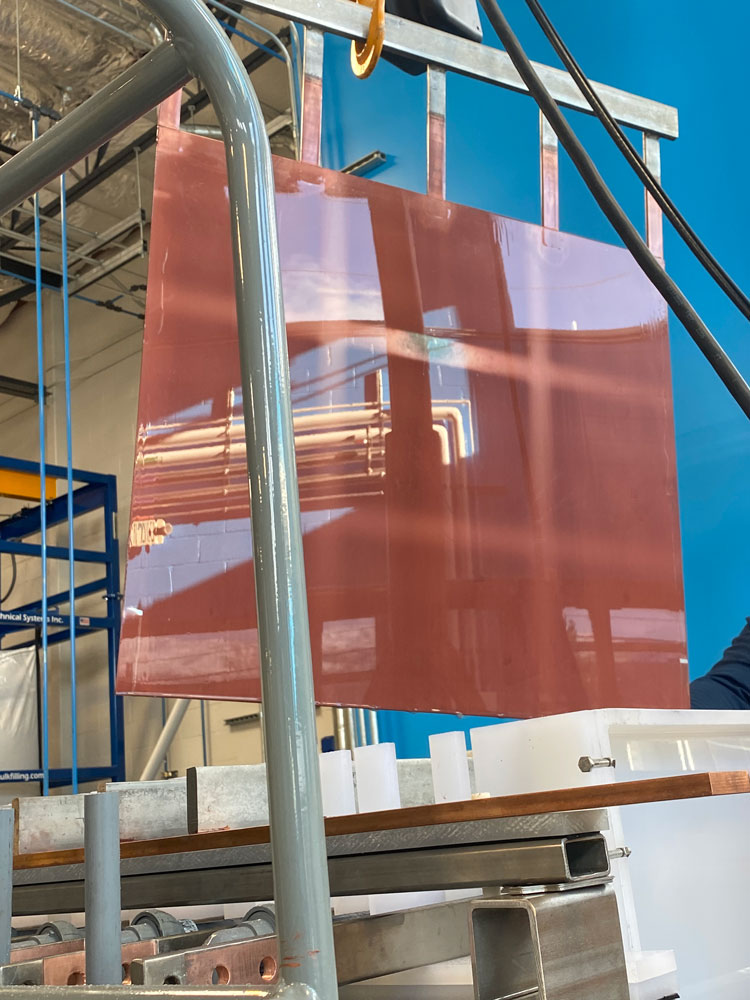
Electro-hydrometallurgy offers several advantages over traditional methods, including lower energy consumption, which contributes to a reduced carbon footprint, as well as diminished waste generation, minimizing the environmental impact. Furthermore, this technique boasts higher metal recovery rates compared to other methods, making it a more efficient and sustainable approach to lithium-ion battery recycling.
Direct cathode recycling, also called cathode healing or re-lithiation, is an emerging method that aims to streamline the lithium battery recycling process by eliminating the need for intermediate metal extraction, and instead focuses on directly recycling the cathode materials into new cathodes for batteries.
Direct cathode recycling faces several challenges that impede its research and development. First, the method requires precise and discrete separation of the exact type of cathode materials from the rest, which requires significant manual labor. Second, the diversity and intermingling of lithium-ion battery chemistries complicates this recycling process, as each individual chemistry would need a tailored approach for effective recycling.
Direct cathode recycling is typically thought of as a one-to-one process—one specific cathode from one supplier turned back into a comparable product—where other recycling methods are more robust and universal.
Lastly, direct cathode recycling is still a nascent technology, requiring further research, development, and investment to prove out viability and scalability for broader implementation.
What is the best method for recycling lithium-ion batteries?
In conclusion, electro-hydrometallurgy stands out as the most promising solution for lithium-ion battery recycling. Its advantages in universality, energy efficiency, environmental impact, and metal recovery rates make it an ideal choice for a sustainable clean energy future.
Aqua Metals is the only electro-hydrometallurgical lithium battery recycler in North America that is operational and actively recovering valuable metals from lithium batteries. You can learn more about our operations and milestones on our Lithium Pilot Recycling Hub.
As the demand for lithium-ion batteries continues to grow, investing in electro-hydrometallurgy will be crucial to minimizing our reliance on virgin materials and supporting a circular economy.