With Aqua Metals’ recent announcement highlighting the recovery of high purity copper (Cu) from lithium battery recycling, the role of copper in our clean energy future has been in the news lately.
Copper is a vital component in many clean energy technologies, and ensuring a secure, domestic supply of copper for manufacturing and various industries is critical to global competitiveness. It is an amazingly adaptable metal with many applications across the economy.
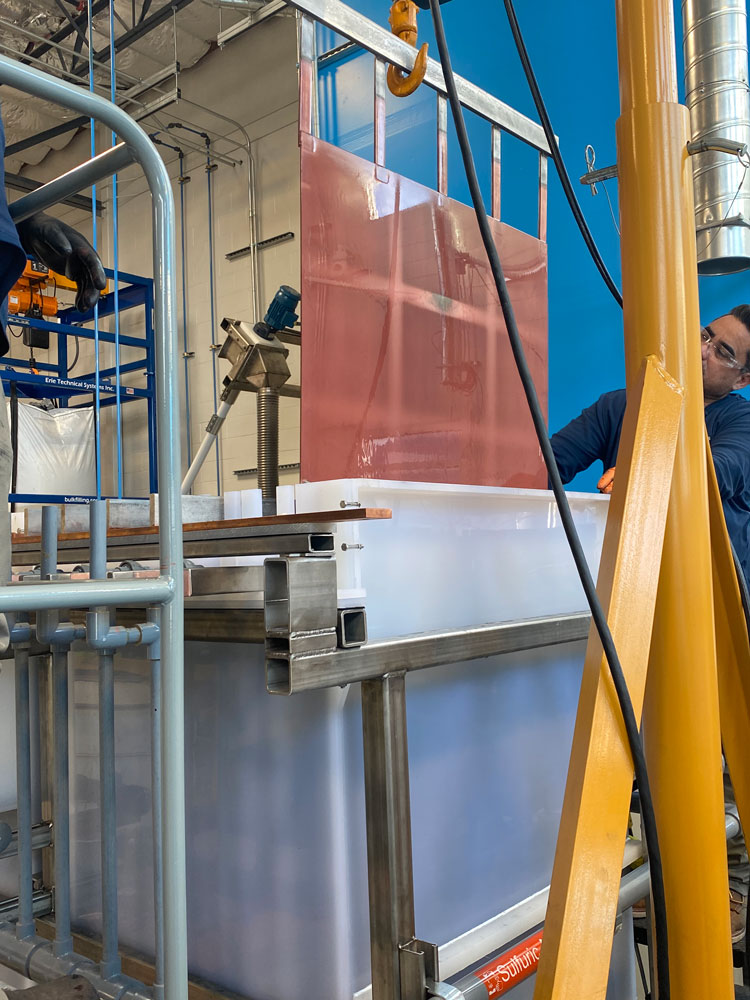
Unlike some other valuable resources, the US does mine a meaningful amount of copper domestically each year – and a significant amount of the total supply today also comes from recycling. Copper itself is highly recyclable and maintains its beneficial properties even when it is reclaimed and reformed multiple times (some of your copper cookware could be the recycled remnants of building wiring from a century ago!)
Globally, we consume about 24 million tons of copper a year, with about 8.7 million tons (~35%) coming from recycled material and the rest from mines. Out of about 2 million tons used in the US each year, roughly 600,000 tons comes from recycling annually.
While copper supplies globally are pretty healthy today, the rapid electrification of the economy is set to strain available resources – adding even more importance to recycling this valuable metal.
Why is Copper Critical
Copper is an excellent conductor of electricity, and this makes it essential for the transmission and distribution of clean energy. In wind and solar power, copper is used among various components and to makes up the wires that transmit electricity generated by the turbine or panel into the electric grid.
Copper is also used to make electric vehicles (EV), which are a critical part of weaning ourselves off of fossil fuels. The red-orange metal is common in motors, wiring, and charging infrastructure for EVs, making it an crucial element of clean transportation. Copper appears in other energy technologies such as energy-efficient lighting, heating and cooling systems, and smart grid infrastructure as well.
As the US pursues ambitious goals for building batteries for homes and vehicles domestically – copper also underpins energy storage technologies like batteries. Copper is necessary for the production of lithium-ion batteries in the form of copper foil which is used in the cathode, and the growing battery manufacturing sector is starting to consume a noticeable amount of copper each year.
This adaptable metal is clearly important for the facilitation of clean energy. Consumer appetite for electric vehicles, energy storage systems and other clean energy technologies is projected to grow rapidly in the coming years, and global demand for copper is expected to double by 2030.
The Old Way of Recycling Copper
Recycling copper conserves natural resources and reduces the energy consumption and carbon footprint compared to mining and refining new copper. Currently, about 35% of the copper that industries consume each year is from recycled sources.
Similar to many other metals, there are two main ways to recycle copper that are popular today. Copper is typically recycled through a process called either pyrometallurgy or hydrometallurgy (or some combination of the two).
Pyrometallurgy: These processes use heat to separate copper from other materials. Scrap copper is melted and then poured into ingots for sale or molds to form new copper products.
Hydrometallurgy: These processes use aqueous solutions to separate copper from other materials. The scrap copper is crushed and then treated with an acidic solution, which dissolves the copper. The copper is then recovered from the solution by various methods such as precipitation, electrowinning, or solvent extraction.
Pyro is a common solution today, but hydro is increasing in popularity due to its ability to more easily separate various metals from recycled e-waste. Both of these processes produce significant amounts of emissions and their own waste from the polluting furnaces and constant supplies of one-time use chemicals.
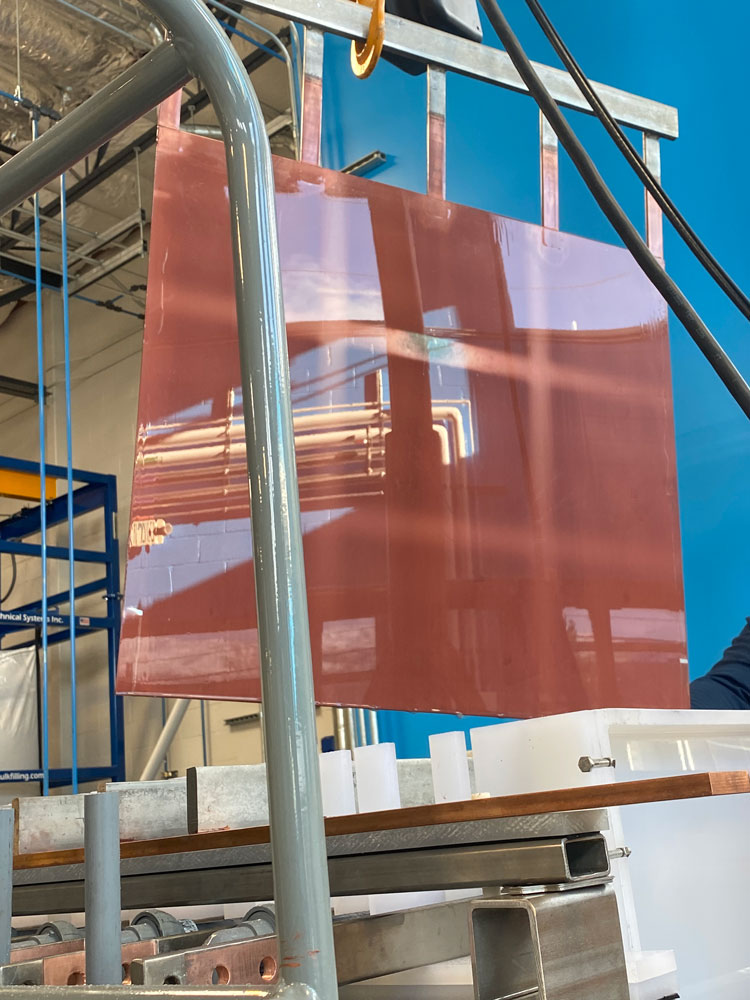
A Cleaner Copper
Aqua Metals’ announcement in January of successfully recovering copper from recycled lithium-ion batteries marks a new era for lithium battery recycling globally. Aqua Metals’ Li AquaRefining technology is underpinned by an innovative application of electroplating – enabling copper to be recycled using electricity, instead of heat or chemicals.
In this photo from our Li AquaRefining Pilot in Tahoe-Reno (January 2023), you can see copper that has been plated when recovered from lithium-ion battery ‘black mass’. (Black mass is the ground up remnants of a battery, with a mix of various metals and materials.).
This represents a step change in both the emissions and the waste produced when recycling valuable metals from lithium batteries – and as we scale operations this will help ensure a secure supply of critical metals requiring about 99% less carbon emissions than pyro-recycling (and 98% less than hydro-recycling).
Other companies are now deploying pyro- and hydro-recycling systems to recover metals from lithium batteries specifically, but those pathways have the same drawbacks no matter what material you are recovering from.
Lithium Battery Recycling: Cu Soon
In the coming decade, the rapid electrification of the economy will strain global copper supplies, and extraction costs will rise as the quality of ore mined continues a steady decline.
Recycling will be critical to ensuring a secure, domestic supply of copper and other metals – but how we recover these resources is equally important.
That is why Aqua Metals is focused on recycling critical metals with electricity, avoiding the emissions and waste of typical recycling methods to get pure metals that can go right back into the supply chain.
At our Li AquaRefining Pilot we are recycling all the metals in lithium batteries with electricity, reclaiming resources like copper with markedly less pollution or waste, and delivering our clean metals back into the domestic supply chain.