A year ago, the United States passed the Inflation Reduction Act, also known as the IRA. This landmark legislation makes tangible the U.S.’s commitment to a clean energy future through investments in the industries and resources that will power a low-carbon economy.
The IRA is focused on the ambitious goal of transitioning from fossil fuels and other polluting energy sources to a fully electrified economy, and while this is predominantly aimed at the country’s energy sector, electric vehicles (EV) and the batteries that power them are also front and center.
As the EV industry begins to accelerate, it is imperative that all phases, from production to end of life and eventually recycling are done sustainably. The government has begun to invest heavily in making sure this is the case, and for good reason – there are widespread economic benefits.
According to a recent Time article from Gina McCarthy, U.S. clean energy companies have begun or announced projects in 44 states since the passing of the IRA, which has produced over 170,000 new clean energy jobs and raised over 278 billion in investments.
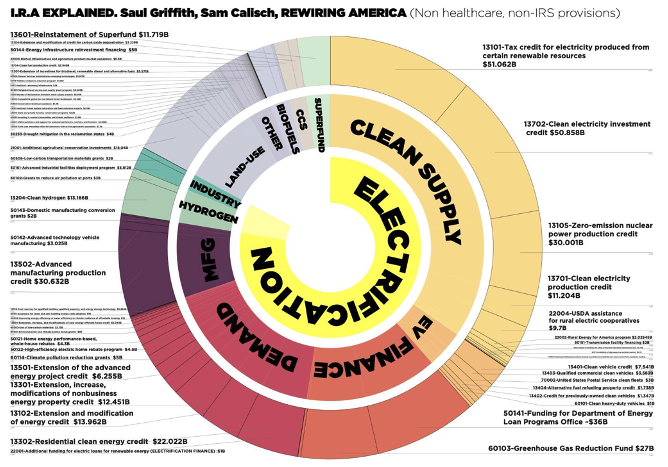
A Need for Material
The recent surge of investment into clean energy and the ever-increasing scale of production of EVs raises the question of where the necessary materials to satisfy this production will come from.
Critical minerals necessary in the production of EV batteries are inherently a finite resource, and the World Bank estimates that meeting targets laid out in the Paris Agreement will require 3.5 billion tons of minerals that will be used for clean energy technologies over the next 30 years.
Although this seems like a lot of minerals, in 2020 alone, we extracted nearly eight billion tons of coal and four billion tons of crude oil for one single year of use. Unlike fossil fuels, which require tens of billions of tons of material to be extracted every year just to be burned – the critical minerals and metals used in batteries can be used and reused nearly infinitely.
Lithium-ion batteries are made from an assortment of critical minerals, like lithium, cobalt, nickel, and manganese. Once an EV battery has been spent and is ready to retire, it’s essential to the production of future EV batteries that those valuable materials can be recovered efficiently and sustainably.
Industry Drawbacks
Unfortunately, the two most popularly commercialized methods of recycling lithium batteries have extremely harmful drawbacks.
The first process, known as pyrometallurgy, involves incinerating batteries in high-heat furnaces. This destroys the lithium and manganese in the batteries and produces low yields, immense energy demands, and copious amounts of carbon emissions and pollution that must be mitigated. Pyrometallurgy clearly does not align with the vision of a sustainable and clean future.
The second process, known as hydrometallurgy, alleviates the need for polluting furnaces but instead utilizes tons of chemical reactions and acids to separate the battery materials. These chemicals are loaded with embedded emissions and create massive amounts of waste material that is subsequently dumped in landfills or even directly into our oceans.
Due to their polluting byproducts and hazardous waste, neither pyrometallurgy nor hydrometallurgy are viable in a climate-constrained world and could put our circular supply chain ambitions further out of reach.
Aqua Metals' Solution
Aqua Metals has developed an alternative method to solve these fundamental problems. Much like the IRA’s goals, we believe the answer to clean battery recycling is found through electrification.
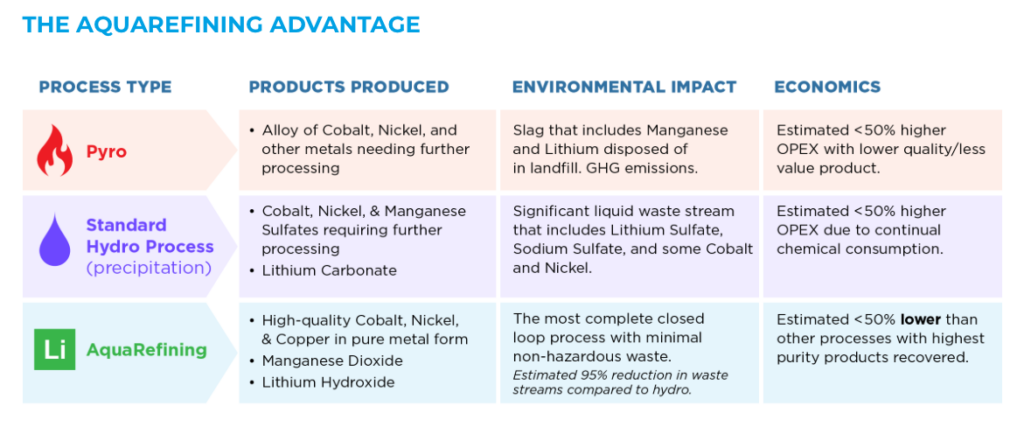
Our recycling process, known as AquaRefining™ ditches the polluting chemicals and furnaces for an innovative process that reclaims critical metals from spent batteries through a method similar to electroplating. With the use of our electrified recycling method, AquaRefining has a clear pathway to net-zero emissions.
Successful electrification requires recycling, and those recycling methods must reflect the IRA’s ambitious goals. As the EV industry continues to grow, it will be important for both suppliers and recyclers to electrify their operations. Aqua Metals serves as an example for others to follow in with our electrified, sustainable process.