Following Aqua Metals’ recent announcement (Feb 2023) as the first battery recycler proven to recover lithium hydroxide in one process at scale, we have received questions about lithium hydroxide and its unique qualities within the battery value chain.
Lithium metal is an essential component of modern technology, and as the demand for electric vehicles and battery energy storage systems continues to grow, so does the need for a domestic resource of critical minerals.
One way to address this issue is by recycling lithium from used batteries, a strategy that can help reduce the environmental impact of the battery metal value chain and decrease sole reliance on mining for material inputs.
However, not all lithium battery recycling methods produce lithium as a recoverable end product, and the choice between lithium hydroxide, lithium carbonate, and other lithium salts can have a significant impact on both the value and cost-effectiveness of recycling methods.
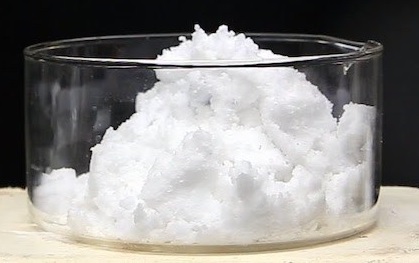
The Many Types to Lithium
Most lithium battery recyclers start with what is called ‘black mass’ – a ground up mixture of cathodes containing several critical metals and graphite anodes from spent lithium batteries (sometimes combined with cathode manufacturing scraps).
By recycling this material, valuable metals such as lithium, copper, cobalt, nickel, and manganese can be recovered and reused to manufacture new batteries. The challenge is to separate these metals from the black mass in a way that is both technically viable and economic.
Notably, recyclers that use smelting technology (pyrometallurgy) to reclaim metals are not able to recover lithium metal due to the oxidation of lithium, aluminum, manganese and calcium that is turned into ‘slag.’ This method was designed to process cobalt and nickel from ore and it was repurposed to process lithium batteries. Originally, the loss of lithium and manganese were insignificant compared to the recoverable value from nickel and cobalt–which is no longer the case with surging lithium values.
Alternatively, one may recover lithium through chemical processes (hydrometallurgy) to create lithium carbonate (Li2CO3). Lithium carbonate is generally recovered via sodium carbonate precipitation, and the sodium sulfate that is generated after precipitation requires landfilling. This is a common solution being considered by recyclers, and lithium carbonate can be further refined into other usable forms of lithium for battery manufacturing applications.
Lithium hydroxide (LiOH), on the other hand, is a more desirable form of lithium that is produced as a monohydrate white crystalline powder and is preferred by many battery and cathode manufacturers. Due to its unique properties, LiOH is an essential feedstock for lithium-ion batteries with a high nickel content (NCA or NMC 811, for example), and is also preferred when preparing lithium iron phosphate (LFP) products by hydrothermal method. Generally speaking, batteries made using lithium hydroxide usually have better performance and longer cycle life than other chemistries.
Other forms of lithium could also be produced through chemical recycling – as lithium salts – and while some are used in speciality battery manufacturing, most have other medical and industrial applications at miniscule volumes compared to demand for lithium-ion batteries.
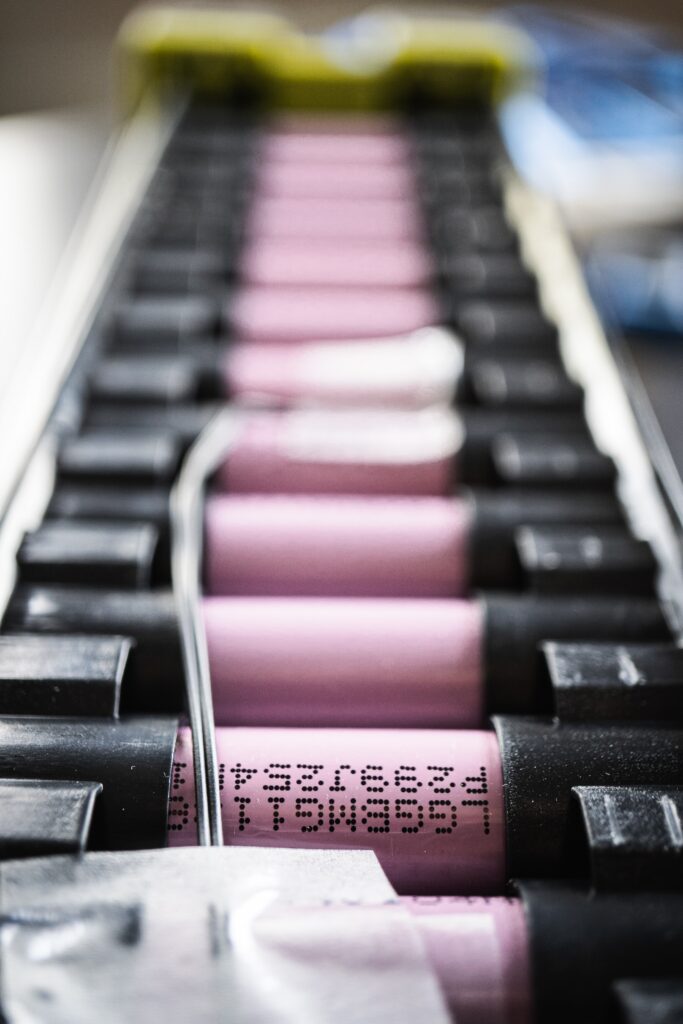
Li AquaRefining: One Step Lithium Hydroxide
Aqua Metals patent-pending process for directly producing lithium hydroxide from black mass is a closed-loop, regenerative recycling system that eliminates up to 95% of the byproducts of other recycling processes. As part of the unique process of creating lithium hydroxide, the AquaRefining system regenerates the solution that the metal is dissolved in – eliminating most byproducts and improving recycling economics even further.
Moreover, by directly recovering lithium hydroxide instead of lithium carbonate or other salts, Li AquaRefining creates a more valuable product with much less waste and no need for additional refinement.
By immediately producing lithium hydroxide, recycling lithium batteries becomes more valuable and more cost-effective by skipping the need for further steps, which would require more energy and produce additional waste. While both lithium carbonate and lithium hydroxide can be produced from recycled black mass, the latter is more valuable and economic in the long run.
As the demand for high-performance batteries increases, the market for lithium hydroxide is expected to keep accelerating in the coming years. Due to its ease of use in manufacturing and electrochemical properties, lithium hydroxide is powering safer batteries that are more efficient and longer lasting. Producing this valuable material from domestic sources helps ensure a circular supply of low-emissions feedstock for use in battery manufacturing across North America.
As the world moves towards a more sustainable future, it is clear that directly recycling lithium hydroxide from used batteries will play a critical role in meeting the growing demand for electric mobility and portable electronics while reducing the environmental impact of the production process.
You can learn more about Aqua Metals’ Pilot recycling facility and track progress on our Pilot Recycling Hub.