Lithium-ion batteries have revolutionized our world. They power our smartphones, laptops, electric vehicles, and much more. But as usage is increasing, so is the need for efficient and sustainable ways of recycling them. While lithium battery recycling offers potential benefits like resource conservation and reducing dependency on raw material extraction, it also brings with it a significant challenge: the production of a copious amount of sodium sulfate and no plans for how to deal with it.
Sodium sulfate, a white crystalline type of salt, is a seemingly innocuous byproduct. It’s used in various industries, from manufacturing detergents and textiles to glass and paper. But when produced in bulk as a byproduct of lithium battery recycling, its limited usefulness is greatly overshadowed by the costly disposal problem it can pose.
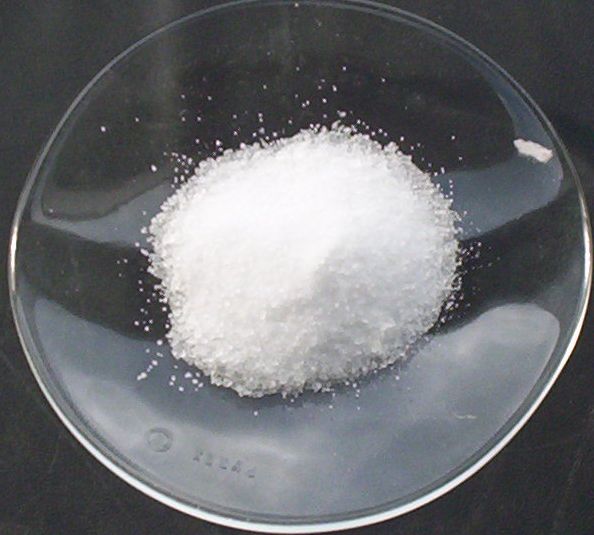
The volume of sodium sulfate produced through some battery recycling processes is certainly surprising. Argonne National Lab’s EverBatt modeling estimates that a typical hydrometallurgy (‘hydromet’) recycling process would produce as much as 800 kg of sodium sulfate for every 1000 kg of battery materials recycled – that’s 80% the mass of what is being recycled is produced as waste!
The crystallizer used to solidify sodium sulfate so it can be disposed of is also very large and costly. Some companies report it is the largest piece of equipment in their entire recycling facility.
Another industry that produces vast amounts of sodium sulfate as a byproduct is ore mining, on account of the chemical leaching processes used to extract valuable metals from rocks. Chemical battery recycling processes – like standard hydrometallurgy – use a similar leaching approach to the mining industry in order to separate the valuable metals contained in spent batteries. But where an ore miner can store tens of thousands of tons sodium sulfate as part of mine ‘tailings’ and waste piles, a recycler does not have the luxury to store tons of sulfate waste on premises. All products from a recycler must eventually be sold for profit or hauled off-site for a cost.
Salting the Earth (and the Oceans)
Solutions for managing this waste from recycling range from the conventional to the absurd. For instance, one commonly proposed method is dumping the material in landfills. However, not only does this exacerbate the already critical issue of landfill shortage, but it also creates potential soil and groundwater pollution risks.
Even more outlandish are proposals to simply dump sodium sulfate waste in the ocean (it is a type of salt, after all). While it may seem like an easy solution, it’s fraught with potential environmental catastrophes. Sodium sulfate can cause harm to marine life, disrupting delicate oceanic ecosystems. (Unfortunately, many battery cathode makers today generally dump their sodium sulfate into the ocean.) It’s an unwise and untenable solution that underscores a lack of sustainable planning.
The production of such substantial amounts of waste highlights a significant problem with our current recycling processes: the creation of tons of worthless and actually harmful byproducts. This predicament undermines the very essence of recycling.
Hydromet recycling requires a constant supply of chemicals used as catalysts for the various recovery processes – and new hydromet facilities often have to connect to train lines to handle the ample amounts of chemicals needed. The byproduct of these chemical reactions can include a number of waste chemicals, but sodium sulfate is one of the most common and most voluminous.
Pillars of Salt
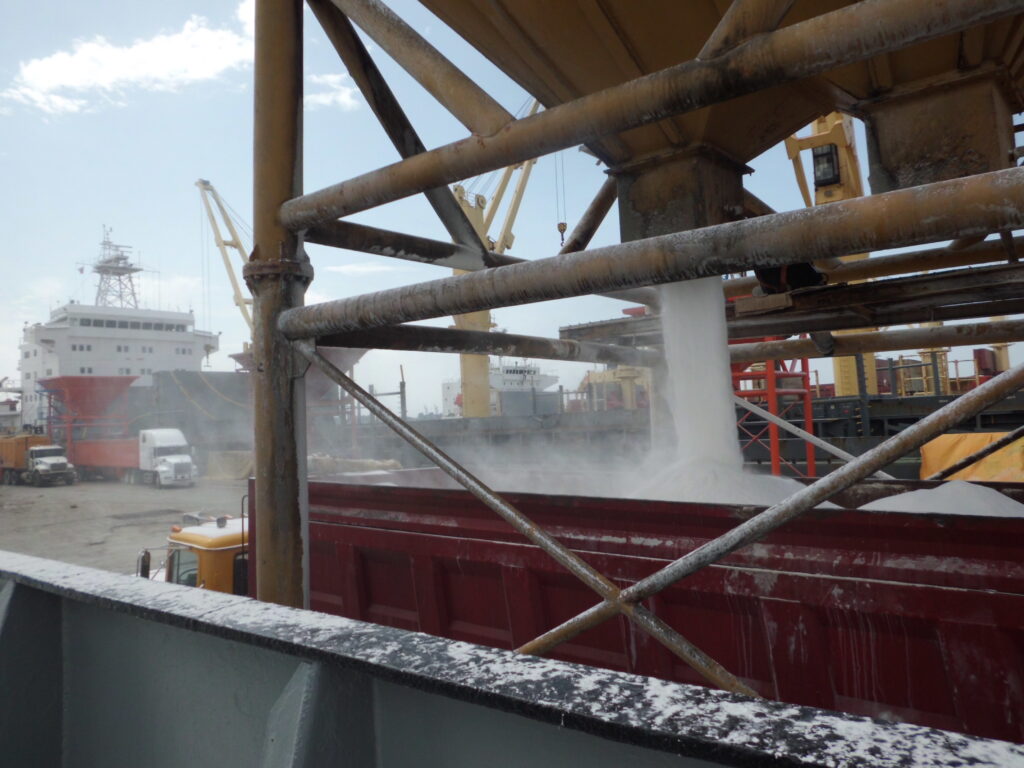
Ideally, recycling should be a circular process, with materials being reused in a sustainable manner. However, when recycling generates vast amounts of unusable waste, the process becomes less circular and more linear, starting to resemble the wastefulness of our traditional ‘take, make, dispose’ economy.
Some researchers and companies are exploring the possibility of utilizing sodium sulfate in new ways. For instance, it could potentially be used in thermal storage systems due to its ability to store heat effectively, or it could be used in novel ways in the construction industry. But these solutions are still in their infancy and require more research and development before ever becoming a practical reality – and the sheer volume of this material produced will soon dwarf the global demand for current useful applications.
Don't Spill the Salt
This dilemma begs the question – Is there a viable solution to the sodium sulfate problem in recycling?
It’s crucial for us to rethink our current trajectory for lithium battery recycling. We need innovative processes that prioritize the minimization of waste, not just the extraction of valuable components.
First and foremost, Aqua Metals’ patented AquaRefining™ process forgoes these chemical catalysts and instead uses electricity as the catalyst for reactions. This means no constant supplying of chemicals needed (also eliminating the embedded pollution and emissions that comes along with them) and no sodium sulfate waste as a byproduct. And in a climate-constrained world, using clean electricity as the primary reagent in battery recycling provides a clear pathway to net-zero operations in the future.

AquaRefining is also a closed loop, so the solvents that are used are regenerated as part of the recovery process, reducing the environmental impact and lowering operating costs. Not only are trainloads of chemicals expensive, but dealing with the waste brings additional costs and pollution. While a small portion of solvents used in AquaRefining will be lost in the filtering process, the automated and closed-loop system reduces chemical consumption by up to 95% compared to hydromet recycling processes – and entirely eliminates the resulting sodium sulfate waste.
Sustainable Lithium Battery Recycling
In essence, the sodium sulfate problem underscores the complexities of the battery recycling process. It’s a stark reminder that even well-intentioned efforts can have unintended consequences, and that truly sustainable solutions require a holistic and forward-thinking approach.
As we strive to make our world more sustainable, it’s essential that we continue to innovate and refine our recycling infrastructure and processes, ensuring they are truly part of the solution, not adding to the problem.