By David Regan, VP of Commercial
We are riding the tipping point in electric vehicle adoption. Following a recent ruling from the California Air Resources Board, by 2035 all new cars sold in California will be zero emission, which likely means predominantly lithium-ion powered. Massachusetts has already declared its intent to follow California’s lead and considering that at least 15 states have previously adopted California’s vehicle standards on clean-car rules, it is likely more states will follow.
In turn, it can be argued that policy is following industry trends. With an 80 percent year-on-year increase in 2021 and projections topping a $1 trillion market size by 2028, it’s clear that EVs are taking to the road in ever more significant numbers.
There is no going back, only forging a smart path forward.
Weaning ourselves from a fossil fuel addiction and addressing climate change are the goals of electrifying transportation, replacing the gas tank with a battery to store motive energy. The implications of this shift require a clear-headed approach to the decisions we make right now.
If lithium-ion battery (LIB) technology is the backbone of the ongoing energy and EV transition, how we source and recycle the minerals used to make the batteries is fundamental for sustainable success. This is not just a future challenge; there is already a large and rapidly growing supply of LiBs, meaning it is vital right now to build a cost-effective, scalable recycling infrastructure that is environmentally sustainable from inception.
The Reality of Recycling
Two interconnected realities inform the lithium-ion battery supply chain’s future economic and environmental viability.
Firstly, the supply of virgin mined material will not meet either near- or long-term future LIB demand as we scale battery manufacturing in the coming years to meet the tsunami of demand resulting from not just the electrification of transportation from cars to golf carts to forklifts, but the rise of stationary application uses as well, including grid scale storage, data centers, consumer electronics and tools.
Other countries control most of the mines producing these strategic minerals, and mining for LIB metals is often burdened with social and environmental ills. With lead-acid batteries, recycling, AKA urban mining, provides up to 90% of the metal in new batteries due to the cost and availability of mined lead, whereas recycling makes up close to 0% of raw materials currently used in LiB manufacturing. Secondly, the method of LIB recycling is as important as the concept from an environmental perspective. Lithium-ion battery recycling processes currently under development fall into two buckets: pyro and hydro.
Pyro, also called smelting, is a straightforward process using heat to extract metals (think “blast furnace”). Smelting is dirty and dangerous, one of the most pollutive activities caused by mankind; truly the antithesis of the EV revolution. It makes little sense to recycle lithium-ion batteries using a process that produces high carbon and particulate emissions, toxic wastewater, and slag. When we reach the expected large-scale volumes of spent LiBs in the coming decades this approach will be unsustainable.
Standard hydro processes use an exorbitant amount of chemicals, instead of heat, as the recycling reagent. These chemicals are very costly and produce a consequential carbon footprint along with significant chemical waste stream byproducts. This approach is also unsustainable long term.
By contrast, AquaRefining is a low emissions, closed-loop method that does not rely primarily on a constant flow of chemicals or heat to recover the high value metals, but on renewable electricity instead.
AquaRefining uses electrolysis to rebuild high purity metals. Chemicals used in the process are recycled, reducing waste streams and the expense of purchasing replacement chemicals.
LIB Recycling Options by the Numbers
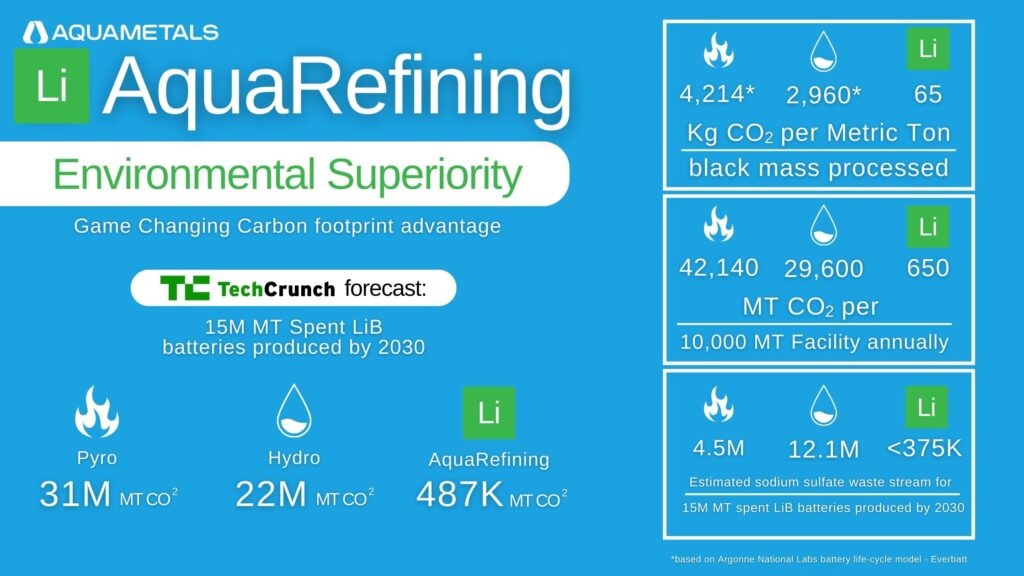
The chart above shows CO2 emissions and sodium sulfate waste streams from pyro and standard hydro recycling, in comparison with AquaRefining.
TechCrunch forecasts 15 million metric tons (MT) of spent LIB batteries by 2030. Let’s break down the numbers based on those projections and data from EverBatt, a closed-loop battery recycling cost and environmental impacts model from Argonne National Laboratory.
Carbon Dioxide Emissions per Metric Ton of Black Mass
Pyro-based recycling produces 4212 kilograms of CO2 for every metric ton of black mass processed. One metric ton of black mass processed through standard chemical hydro emits 2,960 kg of CO2. This is significantly better than pyro. Nonetheless, the process generates nearly three metric tons of CO2 for every metric ton of product.
Aqua Metals’ internal estimates indicate that AquaRefining produces 65 kg CO2 emissions for every metric ton of black mass produced. That converts to 0.065 MT per 1 ton of black mass.
Annual Emissions for a 10,000 Metric Ton Recycling Facility
The following numbers reflect metric tons of CO2 emissions for each recycling method processing 10,000 MT of black mass annually, a typical commercial-sized facility
- Pyro: 42,140 MT CO2
- Standard Hydro: 29,600 MT CO2
- AquaRefining: 650 MT CO2
15 Million Metric Tons by 2030
Recycling TechCrunch’s projection of 15 million metric tons of used batteries by 2030 results in the following CO2 emissions:
- Pyro: 31,605,000 MT CO2
- Standard Hydro: 22,200,000 MT CO2
- AquaRefining: 487,500 MT CO2 = Orders of magnitude less.
Estimated Sodium Sulfate Waste Stream
The sodium sulfate waste stream created from recycling 15 million MT of spent batteries flips the script between hydro and pyro, with AquaRefining still the clear winner:
- Pyro: 4,500,000 MT in landfill
- Standard Hydro: 12,150,000 MT in landfill
- AquaRefining: <375,000
These numbers quantify the narrative previously outlined: Lithium-ion battery recycling is critical to the success or failure of the EV revolution. How we do it is even more important than doing it at all.
AquaRefining recycles black mass at a lower cost with orders of magnitude less environmental impact.
Getting to Scale
A good idea remains only that until proven at scale. Then it becomes a solution. The pyro process is currently the only solution for recycling lithium-ion batteries but is environmentally unsustainable. To date, there are no successful commercial-scale hydro facilities in operation and data shows this process has significant environmental and economic challenges. While AquaRefining is still in development, Aqua Metals is making steady progress toward taking it beyond the idea stage and into the best solution for recycling lithium-ion batteries. That reality is coming into increasing focus, with our pilot plant becoming operational at our Innovation Center in Nevada in November 2022.
Data collected from the pilot will provide further proof of concept, verify emissions and waste stream estimates, and pave the way to full-scale deployment.
The pace and drive of our team reflect the urgency of the challenge.
Navigating the Future
We are on the brink of systemic economic, environmental, and social change. Solving the climate and sustainability crisis hinges on how we respond to the challenges they bring. Electrifying transportation is a massive necessary step to address climate change, but we must not lose sight of the processes and technologies that are needed to support and sustain the shift.
At Aqua Metals, we believe that the only way to meet global emissions targets is not only to electrify transportation but also to recharge the batteries used with renewable electricity and recycle those batteries with renewable electricity.
Effectively replacing the gas tank with a lithium-ion battery means making the right choice today as we build out the energy economy and infrastructure of the future.